Products
RA Series

RA-4300FG+
RA-4300 is an automated, Reducing Vaporization – Gold Amalgamation – Cold Vapor Atomic Fluorescence Spectroscopy (CVAFS) mercury analyzer from NIC to provide Ultra-Trace Level of Mercury Analysis.
Applications
Rainwater, seawater, and any water samples require a sub ppt level of mercury measurement
Methods
USEPA 1631e | USEPA 245.7 | ISO 17852 | EN-1483
Features

QA/QC Validation Program – Put Your Mind at Ease with EPA 1631e Requirements
The operating software of RA-4300FG+ comes with the USEPA 1631e comprehensive formal quality assurance and control package set as per method criteria as default. Users can adjust the limits in accordance with their laboratory criteria, if necessary.
(a) Calibration
(b) Initial precision and recovery
(c) Analysis of blanks
(d) Matrix spike/matrix spike duplicate analysis
(e) Ongoing precision and recovery
(f) Quality control sample
(g) Method detection limit
RA-4300FG+
- Automating the “Purge & Trap Oxidation”
RA-4300FG+ is ingeniously engineered to the requirements of EPA 1631E.
Sample digestion and oxidation processes are automated:

- Dispensing of Bromine Monochloride (BrCl), a strong oxidizing agent, into the sample solution, oxidizing all forms of mercury into ionic mercury.
- Allow setting of incubation time for the oxidation to take place.
- Excess oxidant is destroyed by Hydroxylamine Hydrochloride (NH₂OH.HCl), followed by reduction using Tin (II) Chloride (SnCl₂) to convert all ionic mercury into elemental mercury, Hg⁰.
- The elemental mercury is purged and collected/purified onto a Gold Trap.
- Collected mercury is thermally desorbed and transported by Argon carrier gas into the optical path of CVAFS for measurement.
Extremely Clean Analysis Environment
- Built-In Mercury Removal Filter
Ultra-trace level of mercury analysis requires demanding cleanliness of ambient condition, especially environmental air.
RA-4300FG+ is designed with a clean chamber concept with an integrated innovative Carbon-Layered-Mesh mercury removal filter. All ambient air goes through this mercury removal filter, removing both micro-dusts and mercury where only mercury-free air is introduced into the system chamber.
This feature ensures all samples in sample tubes are kept clean at all times throughout the analysis process.

Superior Detection Limit and Sensitivity
– Detection Limit Down to 0.05 ppt
RA-4300FG+ is equipped with the latest and ultra sensitive CVAFS available which has detection down to 0.05 ppt (0.5 ppt including sample digestion process of EPA 1631e) with excellent accuracy and precision.
With this superior detection limit and excellent precision, the RA-4300FG+ is capable to satisfy a wide range of analysis applications such as snow water, seawater, rainwater and underground springs where mercury contents are in ultra-trace level.
High Productivity
- Autosampler with 80 Positions
RA-4300FG+ is equipped with an autosampler of 80 positions which maximizes the throughput of any fast-paced laboratory, providing results with the shortest turnaround time possible.
Superior Reducing Vaporization by Discrete-Direct-Purge Technique
Generally, there are two methods of Reducing Vaporization, i.e.,
- Flow Injection Technique
- Discrete-Direct-Purge Technique.
All mercury analyzers in NIC employ Discrete-Direct-Purge Technique to minimize memory effect from mercury which causes cross-contamination issue.
Lower Operation Cost
– Reduced Consumption of High Purity Reagents
When it comes to ultra-trace level of mercury analysis, the purity of reagent plays a vital role to have minimum interference to the analyte measurement. Consumption of reagents directly relates to the daily operating cost. By having the discrete-direct-purge technique in RA-4300FG+, all reagents used are reduced proportionally.
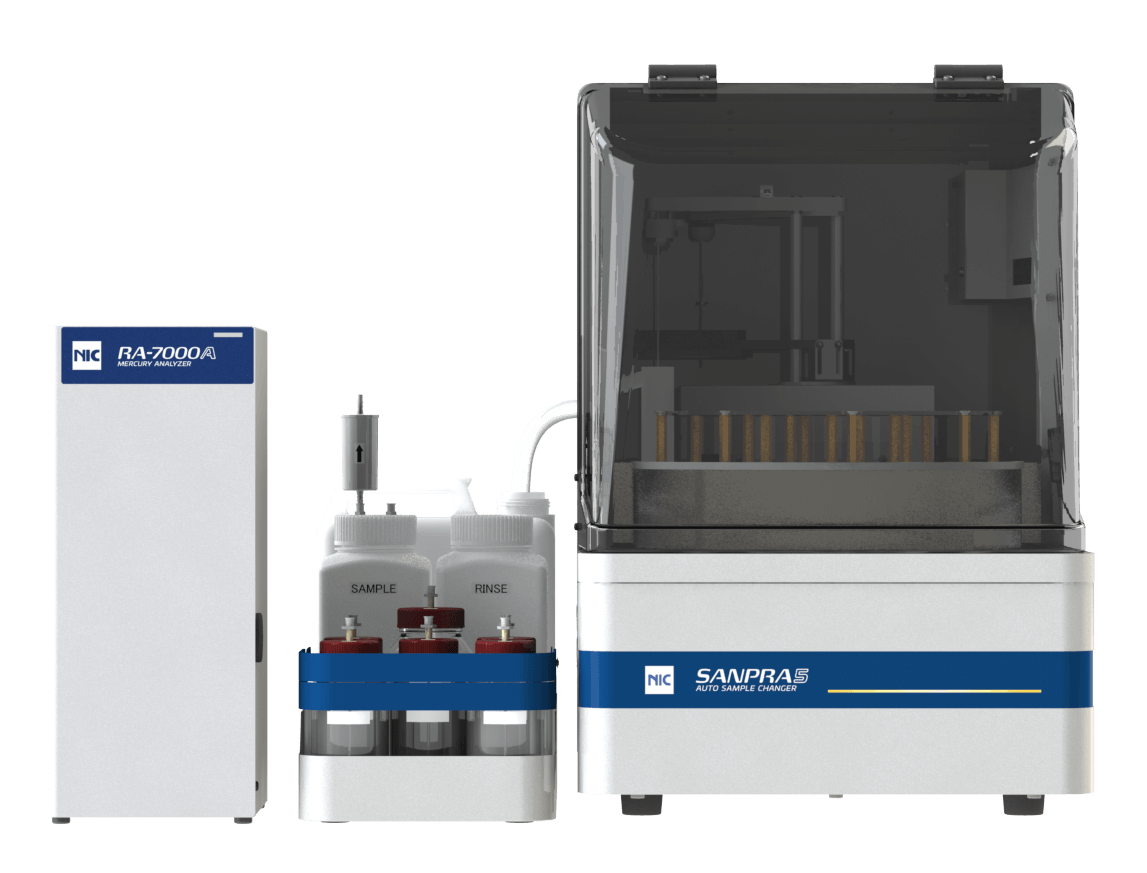
RA-7000A + SANPRA™
Other Series
MA Series
A state-of-the-art Direct Mercury Analyzer
- No sample digestion needed
- Fast analysis time
- Highly accurate
- Solid , liquid, gaseous matrices
PE Series
In full compliance with UOP-98-20, PE Series can fulfill all analysis requirements of liquid hydrocarbon samples.
WA Series
Mercury analyzer for ultra-trace level analysis in gaseous matrices. Featuring Dual Gold Amalgamation technique and various capacity options.